The function of the electrodes is to conduct the current and to withstand the high pressures in order to maintain a uniform contact area and to ensure the continued proper relationship between selected current and pressure. Uniform contacting areas should therefore be maintained.
Good weld quality is essential and depends, to a considerable degree, upon uniformity of the electrode contact surface. This surface tends to be deformed (mushroomed) with each weld. Primary causes for mushrooming are too soft electrode material, too high welding pressure, too small electrode contact surface, and most importantly, too high welding current. These conditions cause excessive heat build-up and softening of electrode tips. Welding of today´s coated materials also tends to contaminate the face of the electrodes.
As the electrode deforms, the weld control is called upon to “step” up the welding current in order to compensate for “mushroomed” weld tips. Eventually, the production line will have to be shut down in order to replace the electrodes or to manually go in and hand dress the electrodes. This process will improve the weld cycle but in either case, the line is stopped and time is lost. Furthermore the deformed electrodes have caused unnecessary high consumption of energy and electrodes.
The dressing can be done after each working cycle. It depends upon how many spot-welds are done in each cycle. For welding in galvanized sheet, dressing after about 25 spot-welds is recommended.
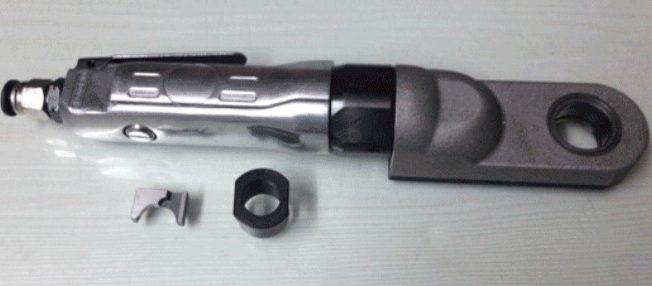
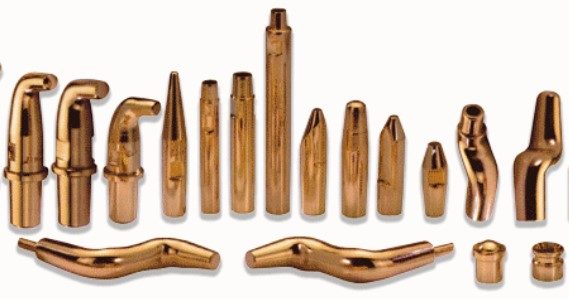
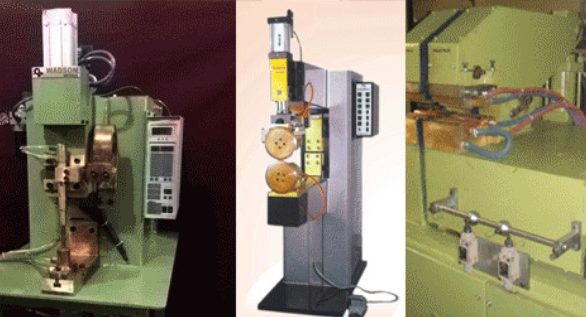